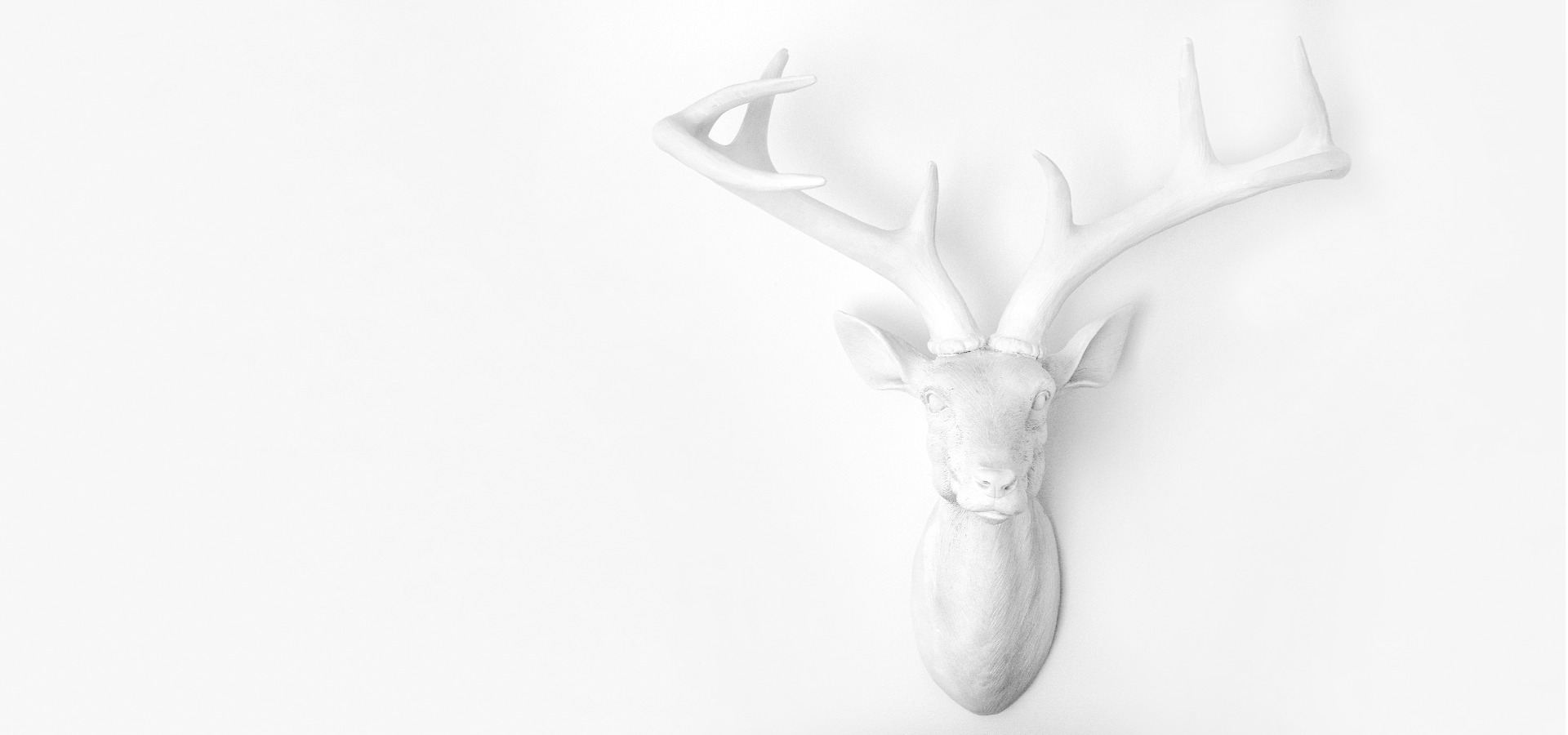
RM Borehole and Well Hand Pumps
R&D
Designed and Built by a Humanitarian Engineer for the Humanitarian Sector
It is far easier to make something that is complex than simple - especially when the product has to have exceptional performance and durability at a competitive cost. I first started to discuss ideas with colleagues on a completely new design of hand pump in 2007. Since then hundreds of hours of brainstorming came up with a range of ideas - some of which we experimented with. In the car racing industry it is said that most prototypes end up in the scrap bin. It is most certainly true in our case.
In 2016 R&D started in earnest. Once one throws a significant amount of time and money at something there is no going back. 2 years of experimentation was put into a different concept to our final product. It used a diaphragm. It was made to work but we decided that it was too complex with too many parts.
The greatest amount of time and patience goes into field testing. There are no shortcuts. We had a large diameter well and a deep borehole drilled close to the workshop. The prototypes are power-driven at 1 stroke/second, 24-7 for 6 months after which wear and output are gauged. We adjust the pressure output to simulate performance at lift heights up to 30 m. As at 18th April 2019 the latest test model has completed 5.2 million pump strokes and pumped 1.4 million liters of water with no problems and 100% sustained output/stroke.
6 months continuous operation is roughly equal to 3 years operation under average field conditions. We have a policy of continual improvement. Ultimately, we will extend test time at different pressures until something fails - then improve it.
Another consideration relates to transport and installation by technicians who often don't have extensive engineering experience. The bulk and weight of existing pumps requires that pickup vehicles (often with roof racks) are required for field work. Our version had to be light and compact enough for a number of units to fit in the common ambulance type Land Cruiser. This we have achieved.
The greatest compliment someone can give us is, "Gee that's simple". Simple and superior.
M C
06 03 2020
The test unit has been run for 6200 hrs. There was little change in volume output. Inspection of valves shows some wear. All other components display minimal wear. The lift webbing and its guides are particularly durable. We now know which combination of materials are the most wear-resistance.
We decided to change to a different design of valve. We are now testing a heavy-duty stainless steel version. We also decided to address a 30% drop in output when pressure is increased to an equivalent to the range of 12 m - 20 m lift (depth to the water level).
This appears to be due to some leakage past the piston. We proved this by testing a piston with a conventional cup seal, which overcome the output reduction. We are reluctant to use such a seal as these are one of the weak components in current pumps on the market.
The latest R&D involves development of an innovative piston that has an integrated seal created through machining.
I am confident that we could market a very durable pump based on what we have tested over the last 12 months. However, we don't want to just produce the best pump available. We want to produce an exceptional pump with extreme durability.
So, testing continues. The new piston design will require a further 6 months
A complete 20m-lift pump packed for transport. Dimensions: 0.5 m x 0.6 m x 2 m. Weight < 50 kg
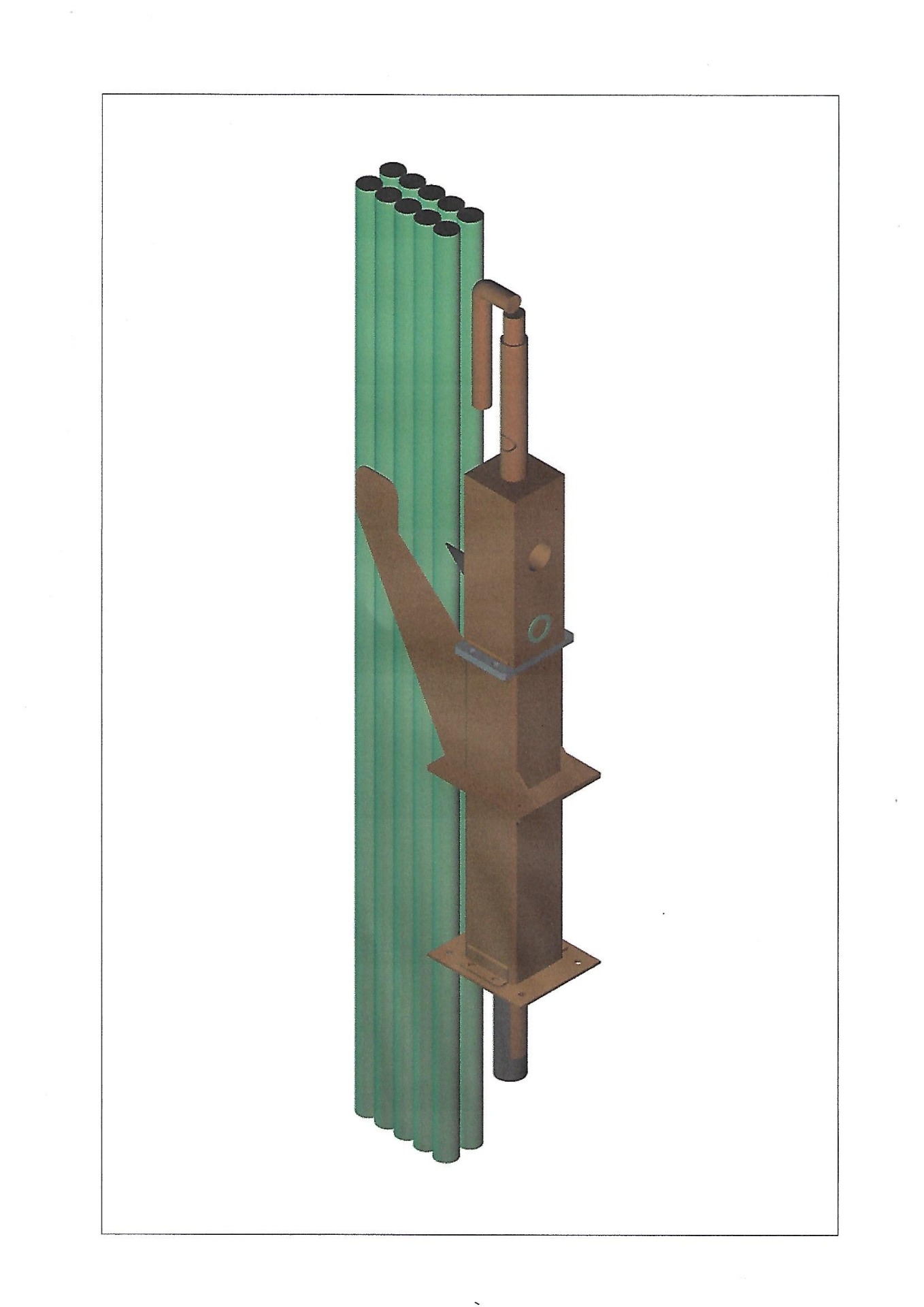